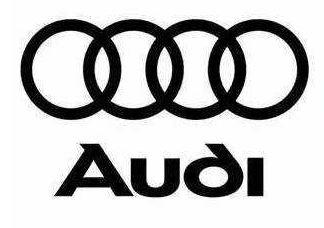
Some of car parts are made in plastic material, and all parts must meet strict safety and heat resistance. This is the reason that only petroleum-based materials are suitable for the production of particularly severely worn plastic parts in automobiles.
In the most cases, these materials are not recyclable. Although the same type of plastic can usually be recycled mechanically, recycling mixed plastic waste is a major challenge.
Therefore, as part of the "Industrial Resource Strategy" think tank, Audi and the Karlsruhe Institute of Technology are launching a chemical recycling pilot project to re-enter these mixed plastic fragments into a resource-saving recycling system.
The goal of the "Chemical Recycling of Plastics in Automotive Engineering" pilot project is to establish an intelligent recycling system for plastics and use this method as a supplement to mechanical recycling and energy recycling. In cooperation with KIT, Audi intends to preliminarily test the technical feasibility of chemical recycling and evaluate the method in terms of economics and environmental impact. These assessments were conducted at KIT by a team led by Professor Dieter Stapf of the Institute of Technical Chemistry (ITC) and Dr. Rebekka Volk of the Institute of Industrial Production. To this end, Audi provides plastic parts that are no longer needed, such as fuel tanks, wheel trims and radiator grilles, which come from Audi models returned from the German dealer network. These plastic parts are processed into pyrolysis oil through chemical recycling. The quality of this oil is comparable to that of petroleum products, and the materials made from it are as high-grade as new materials. In the medium term, parts made from pyrolysis oil can be used in automobiles again.
Chemical recycling is the only method that can be used to convert this mixed plastic waste into products of comparable quality to new plastics. Therefore, more types of plastics can be recycled. This closed material cycle has several advantages. They save valuable resources because fewer raw materials are required. This in turn saves energy and costs, and is good for the environment. Audi was one of the first automakers to test this recycling method in a pilot project for plastics in automobile production. "So far, the recycling of automotive plastics has not been realized in many parts.
This project was established in KIT by the think tank "Industrial Resource Strategy" supported by the Baden-Württemberg state government, industry and academia. "Think tanks focus on looking at the recycling of raw materials as a whole. Chemical recycling is an important part of comprehensive plastic recycling. This makes it an interesting proposition in the automotive industry. Think tanks and Audi are working together to solve a core problem, which is to make cars in the future In its development, regardless of the type of power system, it is more sustainable and environmentally friendly," said Dr. Christian Kühne, general manager of the think tank.
Together with its suppliers, Audi uses chemical recycling as part of the CO2 workshop. The goal of Audi's carbon dioxide project is to use resources as efficiently as possible and reduce carbon dioxide emissions in the upstream value chain, clearly focusing on materials that require large amounts of use or require particularly energy-intensive production processes. A successful case is the "closed loop of aluminum industry". Audi and its suppliers used this closed loop to successfully recycle aluminum scrap and improve it to the quality level of new products, thus avoiding the environmental balance sheet in 2019 alone.
In the future, textile seat covers for all model series should be made of recyclable materials. If its technical feasibility can be proven, Audi plans to industrialize the technology and gradually apply it to more components.
Posted By Leila
Email:[email protected]